It seems at times that the amount of wiring in the 90 just keeps going up and up and up ! This last weekend I’ve had the dash apart again, hopefully for the last time before it ships…
I wanted to add a couple of isolation switches both for safety and also to ensure that the batteries will make it to the other side without being discharged. I wanted to add an isolator for each battery so they could be isolated individually. If nothing else this means I can leave the auxiliary battery disconnected so if the main battery gets left on during shipping we can jump start it from the auxiliary battery. Positioning the switches so they are accessible from both seats and at the same time reduce the risk of them being accidentally switched off took some thinking about and in the end we settles for a position next to the passenger seat. The main battery switch is an FIA type which has the extra contacts that I’ve wired in so that the switch will also kill the engine if turned off with the engine running.
I have rewired the switches for the spotlights and the rear work lights – the rear work lights were connected to a Carling switch on the dash and the spotlights to the Land Rover spotlight switch. This was OK but didn’t give too many options for the spotlights and, as they are LEDs and can be left on for long periods without draining the battery, I wanted a switch that would allow them to be turned off, on only with main beam and on independently. To achieve this I changed them around using a Carling switch for the spots and the Land Rover dash switch for the rear working lights.
With the Dash apart I changed the iPad RAM mount from the seat mounting type to a universal mount on the dash. The seat mount is OK but tends to wobble around all over the place when you’re crossing rough ground, so much so you have to lock the rotation on the iPad. The dash mount takes up less room and will stop the annoying wobbling !
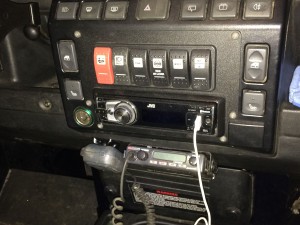
Australian CB Radio
I also added an LED interior light for the passenger area that works in addition to the factory interior lights and fitted the mount for the UHF radio (Australian CB radio), connected up the power lead for the radio and the aerial lead. I also got around to fitting the map light to the top of the dash. All in all a busy few days and lots of jobs “ticked off” the list in the process 🙂